Acceleration from 30 shipments to 200 per hour. DB Schenker deploys fleet of robots in new giant warehouse
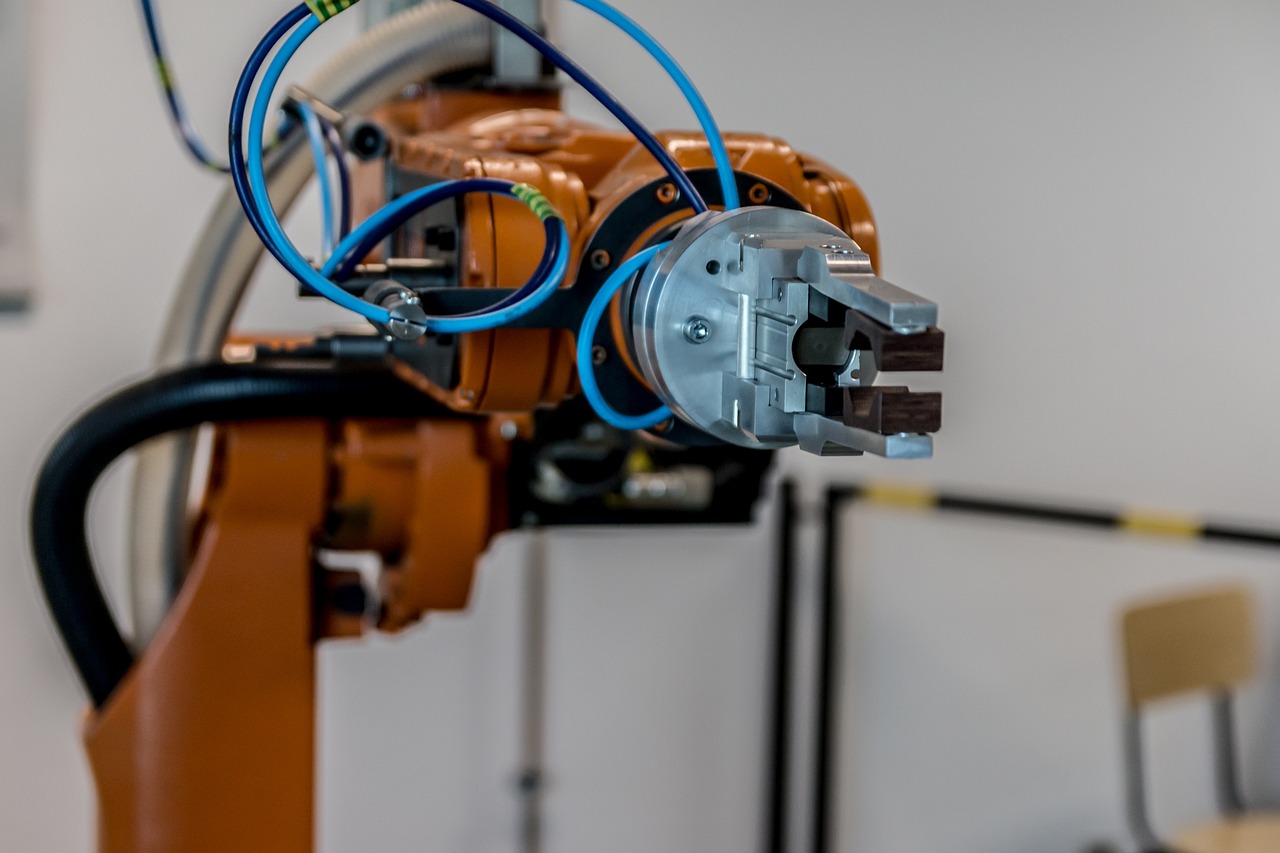
Think of them as the oversized robotic vacuum cleaners that normally help us around the house. But these helpers do a lot more and are much more powerful. Each robot can carry up to 500 kilos, making it easier for people to work in DB Schenker’s state-of-the-art logistics centre.
One of the world’s largest and oldest logistics companies, DB Schenker, has been operating in our country for 30 years. And it is in the Czech Republic that the company is launching its world’s most modern warehouse in July, with one of the largest deployments of robots in Eastern Europe.
Preparations are now being finalised in Rudná near Prague. The move from the existing premises to the new ones must be carried out in a flash, without any disruption to operations. The whole project took about two years. The construction, which was preceded by careful preparation, began last November and the use of modern technologies was already in mind when designing the project. In this respect, the warehouse in Rudná ranks among the absolute top not only in the Czech Republic, but also in global comparison.
A large part of the large building is occupied by autonomous mobile robots. Thanks to them, warehouse operators no longer have to walk for miles around the hall or handle heavy shipments; technology takes care of this work. The robots have been designed to be able to move around the designated area on their own, loading and transporting racks full of shipments. They inhabit a 3,500-square-metre space.
Thanks to the built-in QR code-reading cameras, the robot can monitor the markings on the floor and on the individual shelves and use the software to find the optimal path between the shelves, without colliding with its robot colleagues. When everyone is on the move, the hall gets really busy. There are currently 113 robots serving 470 shelves, and the system can be expanded to 220 robots and 1,000 shelves in the future.
A major advantage of deploying technology is the facilitation of human work. The robot itself finds the right rack with packages from suppliers, picks them up and transports them to the so-called picking station, where individual shipments are assembled. The warehouse worker just needs to take the item, which is indicated by a light signal in the rack, and put it into the prepared crate. He doesn’t have to walk around the warehouse looking for the right item, nor does he have to find out which package goes where. The light also shows him when the shipment is complete.
The software itself will evaluate how to bring the racks of packages to the picking station and plan the picking so that transport and handling is as efficient as possible.
The processed shipment can continue on to packing or further clearance. Here too, technology helps, saving you steps and hard work. The backbone of the entire system is nearly 3 kilometres of programmable conveyors that send goods on their way to the end customer according to a barcode placed on the shipment.
The area reserved for the robots is equipped with sensors that immediately stop the machines if a human enters the zone or if any other obstacle is encountered. Other safety sensors are contained directly in the robots. Safety is one of DB Schenker’s top priorities, so it was already considered during the design phase.
The workstations are designed with ergonomics in mind, right down to details such as the appropriate tilt of the shelves at the picking stations. Protective equipment, such as hard-toed shoes, thorough training of new recruits and regular training of staff, not only warehouse workers but also support departments, are all part of the package. Everyone is involved in making the environment as safe as possible.
Source, photo: schenker.cz, pixabay.com
Author of this article
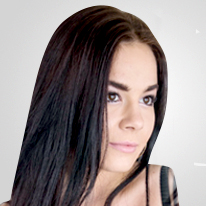
WAS THIS ARTICLE HELPFUL?
Support us to keep up the good work and to provide you even better content. Your donations will be used to help students get access to quality content for free and pay our contributors’ salaries, who work hard to create this website content! Thank you for all your support!
OR CONTINUE READING