New, more efficient batteries for electric vehicles are coming
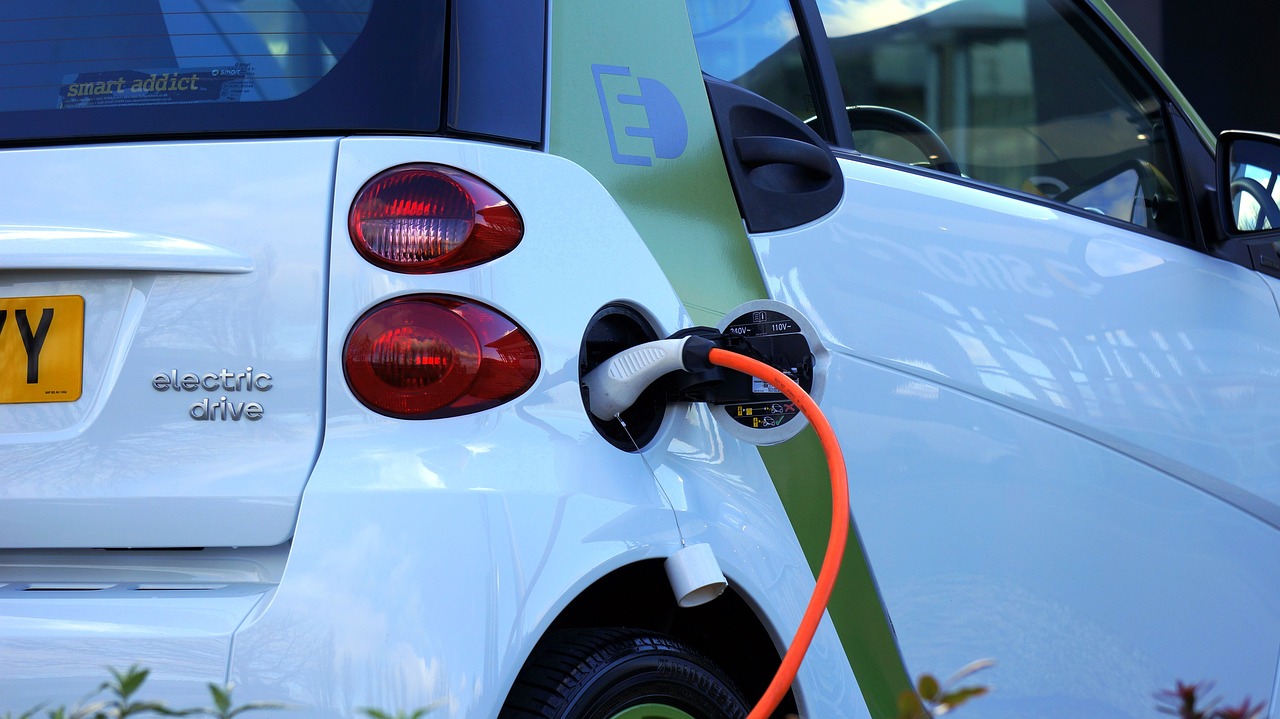
One of the “revolutionary” inventions that technologists (and journalists) have been talking about for years is finally coming to market. But more important than the deadlines is the fact that development still hasn’t stopped. Lithium batteries have been on the market for more than a quarter of a century. In that time, they have changed significantly. However, a close look inside modern batteries would show that progress has been very uneven: it has been on the cathode side of lithium-ion batteries. The graphite anodes of the “lions” have not changed fundamentally.
Meanwhile, replacements for the carbon electrode have been sought for decades. One of the most promising materials for the anodes of next-generation lithium batteries seems to have been silicon for a long time anyway. It can hold several times more lithium ions than graphite. This is one of the reasons why silicon was even used as an electrode in laboratories during the development of “lion cells” – and for the first time a full seven years earlier than carbon. Experiments with this element, however, constantly ran into technical problems. However, after some 15 years of incremental improvements and disappointed hopes, it seems that the “silicon age” has now arrived in batteries.
When lithium-ion batteries are charged, the positive electrode (cathode) of the lithium alloy releases ions. These move to the negative anode, which is usually made of carbon. The ions from the cathode hide in the carbon layers of the anode, where they wait until the battery needs energy. Then the whole process starts to work in reverse: the ions from the anode travel to the cathode, where they meet electrons coming from the other side of the switched circuit.
Today, carbon anodes are used, which have good electrical conductivity but, for physical reasons, very limited capacity. It takes a “cage” of six carbon atoms to hold one lithium ion. If the carbon could be replaced by something more efficient, this could be a significant change. Silicon, which has the added advantage of a wealth of experience in electronics manufacturing, could be extremely suitable. A single atom of silicon can bond four atoms of lithium. This advantage has long been known and silicon has been experimented with extensively, but unfortunately it also has very unpleasant properties.
A significant one is that it “swells” after electron absorption – it changes its volume very significantly, several times, to roughly three times its original volume for simplicity. If you build a battery out of silicon using conventional methods, it only takes a few charges, the anode breaks into small pieces and the whole cell is useless. It’s one of the main widely known obstacles on the road to a possible better battery, and a dead end that many teams have tried. Manufacturers have looked for different ways around the difficulty. A very small number, on the order of one percent, have been using Tesla’s EV cells for years. The admixture is so small that the increase in volume is not a big problem and the increase in capacity of a few percent is worth it.
Group14 and Sila are trying to tame the price by designing silicon materials that behave and look just like the black carbon powder used to make today’s anodes. This, they say, will make it unnecessary to change manufacturing processes. Sila’s silicon powder consists of micrometer-sized particles of silicon and other materials that are surrounded by a porous scaffold of another material. This material allows batteries to be produced with 20 percent higher energy density than batteries with graphite anodes. That can mean about 100 kilometres longer range for most electric cars if you don’t want to get cheaper, or a 20 per cent smaller, lighter and therefore cheaper battery. The choice may depend on the purpose of the car. The company also says it plans to double that value in the future, but let’s get that out of the way first.
Group14 is leveraging its expertise in producing porous carbon materials for batteries and power capacitors. The company produces micrometer-sized porous carbon particles in a single step and a single reaction using a patented process. Silicon enters the pores of this material by chemical vaporization.
The silicon that forms inside is amorphous, not the crystalline kind used by competitors. The company claims that this solution is preferable because it is the most stable form of silicon with a long lifetime. It is not clear which of the technologies will actually take off in the end and which will not. Perhaps all the companies mentioned and a few more will catch on with the “silicon battery” – the market is huge. However, it is already important that such technologies are emerging, even though they may have taken much longer to develop than companies originally claimed.
This indicates that the main process by which we can even think about electromobility or even the use of batteries in the electricity grid has not yet been completed. Even if chemical batteries are not as cheap and accessible as we would like, in the past their cost was astronomical – and that was not so long ago. In fact, when ‘lionesses’ appeared on the market in the early 1990s, they were around 30 times more expensive than they are today. According to a recent study, the price of lithium batteries has fallen by around 97 percent over the past three decades. And what has been behind this rapid price decline?
When a team from the well-known US engineering university MIT looked into this question a few years ago, they concluded that by far the strongest factor was successful investment in research and development, particularly in battery chemistry and materials science.The benefit of these ‘improvements’ was greater than the benefit of economies of scale, i.e. the savings from actually producing batteries on a large scale in optimised plants (but economies of scale were the second largest contributor to price reductions). The findings could reportedly also help in future corporate and national planning in this area.
At the same time, however, the slow take-up of silicon batteries shows that innovation simply takes time. Nowadays, with the way science and R&D in general is funded, this process is faster than ever. Improving the steam engine from a curiosity to a powerhouse that triggered the Industrial Revolution took many decades.
Source, photo: group14.technology, pixabay.com
Author of this article
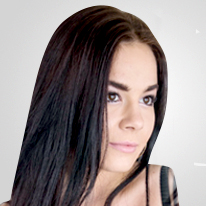
WAS THIS ARTICLE HELPFUL?
Support us to keep up the good work and to provide you even better content. Your donations will be used to help students get access to quality content for free and pay our contributors’ salaries, who work hard to create this website content! Thank you for all your support!
OR CONTINUE READING